How Does OSHA Enforce Its Standards?
The Occupational Safety and Health Administration (OSHA), established under the Occupational Safety and Health Act of 1970, plays a critical role in protecting the health and safety of American workers. By setting and enforcing standards, providing training, and supporting employers and employees, OSHA ensures safe and healthful working conditions. But how exactly does OSHA enforce its standards? Enforcement involves a combination of inspections, citations, penalties, and follow-up procedures that ensure compliance and encourage corrective actions.
The Foundation of OSHA Enforcement
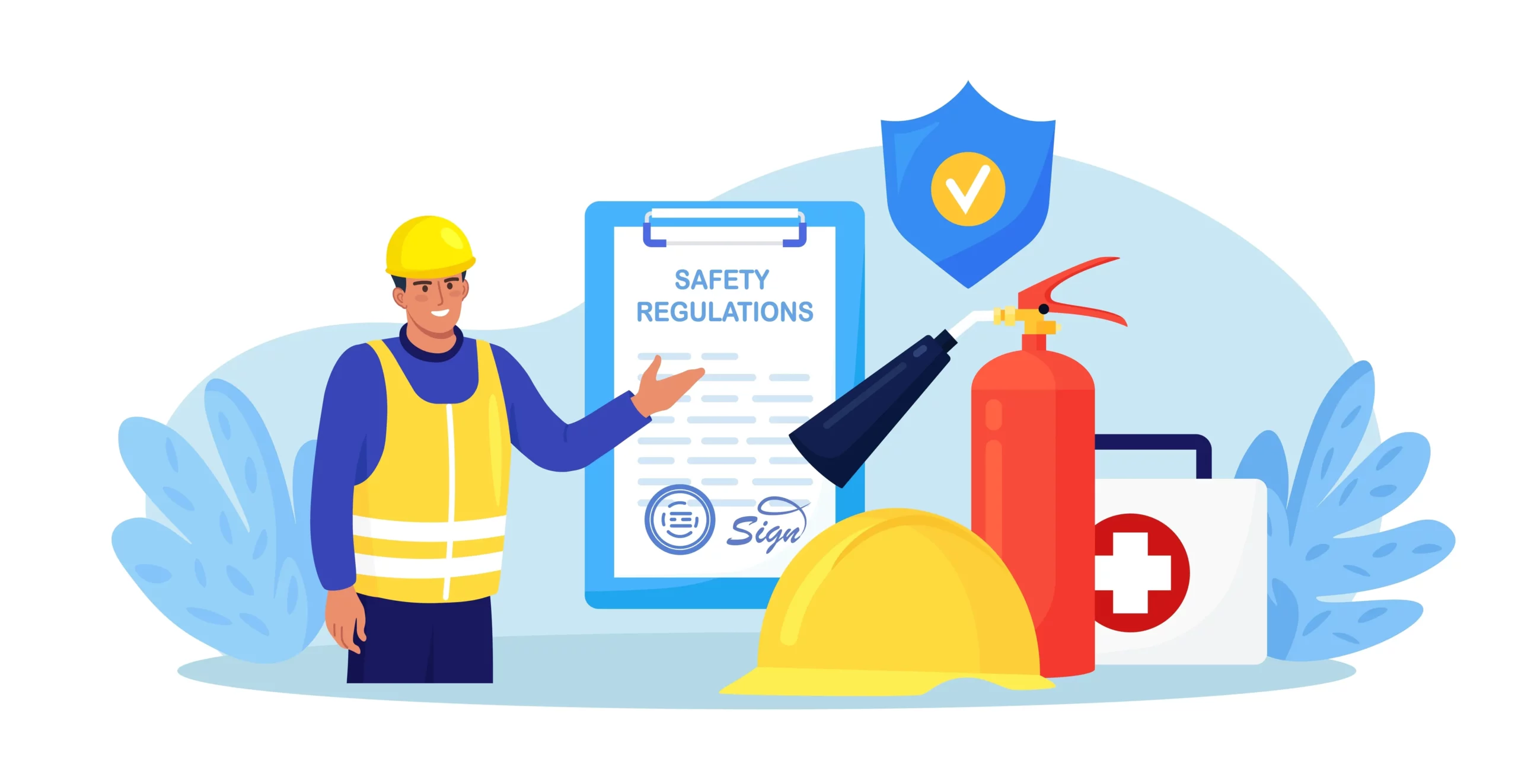
OSHA’s authority stems from the OSH Act, which mandates that employers provide workplaces free from recognized hazards. OSHA standards are legally binding rules that cover various hazards, including fall protection, respiratory safety, electrical safety, chemical exposure, and more.
Enforcement is one of the agency’s most powerful tools for ensuring compliance. It involves proactive inspections, reactive investigations (based on incidents or complaints), and a system of penalties and corrective actions designed to deter violations and promote a safe workplace.
How OSHA Initiates Inspections
OSHA inspections are carried out by compliance, safety, and health officers (CSHOs) who are well-trained in recognizing workplace hazards and applying OSHA standards. These inspections may be unannounced and can be triggered in several ways:
1. Imminent Danger Situations
If OSHA receives a report about conditions that could cause death or serious physical harm, an inspection is initiated immediately.
2. Severe Injuries or Fatalities
Employers are required to report all work-related fatalities within 8 hours and all inpatient hospitalizations, amputations, or losses of an eye within 24 hours. Such reports often trigger an investigation.
3. Worker Complaints
OSHA gives high priority to valid employee complaints. Workers can file confidential safety complaints online, by mail, or by phone, and OSHA may follow up with an inspection.
4. Targeted Inspections
OSHA sometimes targets specific high-hazard industries or companies with high rates of injuries and illnesses.
5. Follow-up Inspections
If a previous inspection resulted in violations, OSHA may return to verify whether corrections were made.
6. Referrals
Other federal, state, or local agencies — or even the media — may notify OSHA of unsafe conditions, prompting a site visit.
The OSHA Inspection Process
An OSHA inspection generally follows a structured process:
1. Presentation of Credentials
The OSHA inspector identifies themselves and presents their official credentials to the employer or representative.
2. Opening Conference
The inspector explains the reason for the visit, outlines the inspection process, and discusses employer and employee rights.
5. Closing Conference
After the inspection, OSHA conducts a closing conference to discuss findings and potential citations. The employer is informed of possible violations and given a chance to provide relevant documentation.
3. Walkaround
This is the core of the inspection. The officer tours the workplace, observes conditions, and talks to employees. They may use monitoring instruments, take photographs, and collect samples.
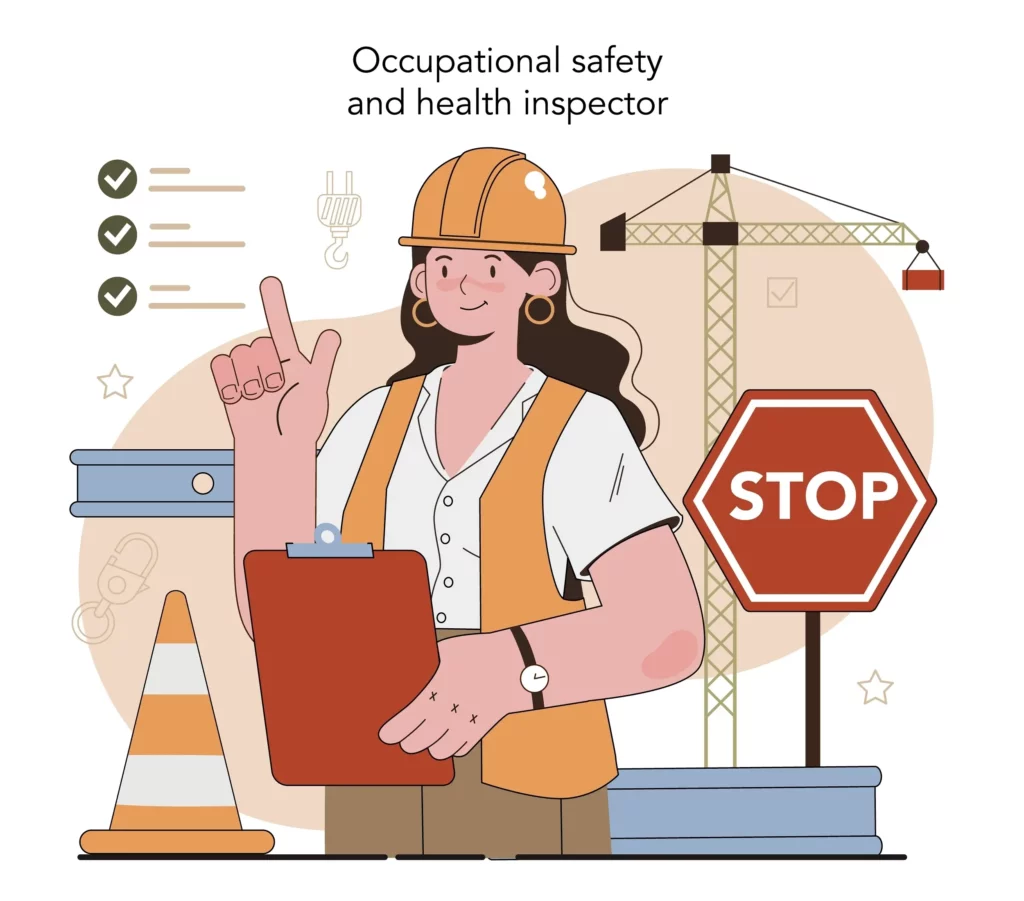
4. Interviews
Inspectors may privately interview employees to understand workplace practices and any safety concerns.
Citations and Penalties
If OSHA identifies violations, it issues citations and proposes penalties. Each citation outlines the type of violation, the specific standard violated, and a deadline for correcting the hazard.

Common Types of Violations:
- Serious Violation: A hazard that could cause death or serious harm and the employer knew or should have known about it.
Penalty: Up to $16,131 per violation (as of 2024). - Other-Than-Serious Violation: Not likely to cause serious harm, but still violates standards.
Penalty: Up to $16,131 (discretionary) - Willful Violation: The employer intentionally or knowingly violated the standard.
Penalty: Up to $161,323 per violation - Repeat Violation: A previously cited issue that recurs upon re-inspection.
Penalty: Up to $161,323 per violation - Failure to Abate: If a previously cited hazard isn’t corrected by the deadline.
Penalty: Up to $16,131 per day beyond the abatement date
OSHA allows employers to contest citations and penalties within 15 working days of receiving them.
Corrective Action and Abatement
Once cited, employers must correct the violation(s) by a specified deadline. They are required to post the citation in the workplace near the area of the violation for at least three working days or until it’s corrected, whichever is longer. Employers must also:
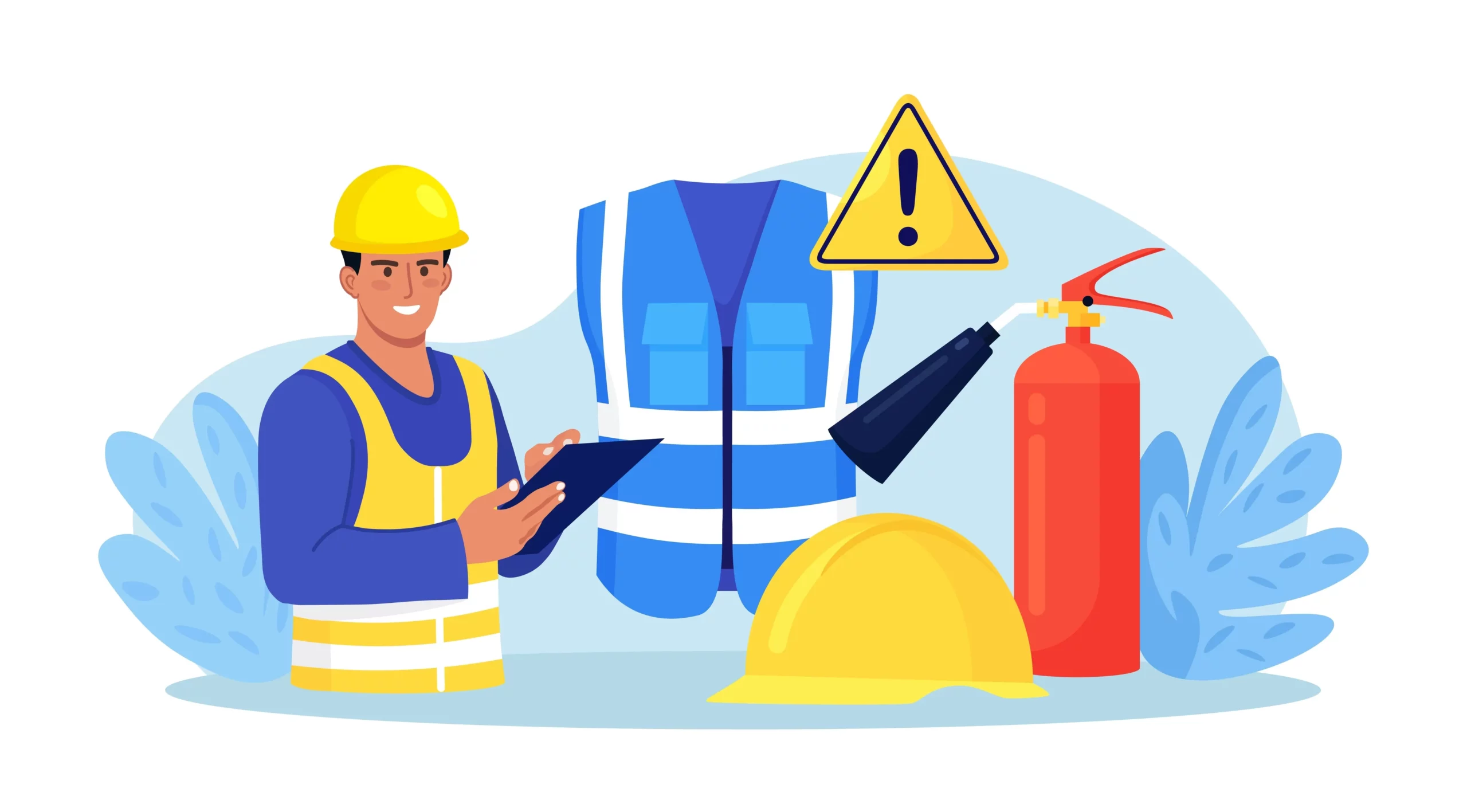
- Submit an abatement certification letter, stating that each violation has been corrected.
- In some cases, provide abatement documentation, such as photos, receipts, or training records.
Failure to correct violations can lead to follow-up inspections and additional fines.
OSHA’s Cooperative Programs
While enforcement is a critical function, OSHA also offers collaborative and educational approaches:
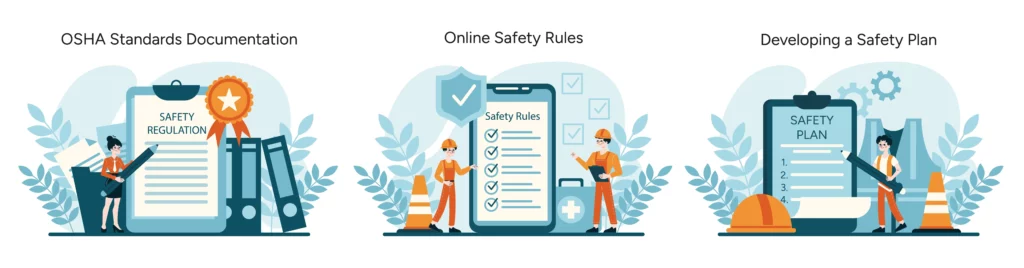
- Voluntary Protection Programs (VPP): Recognizes employers and workers who have implemented effective safety and health management systems and maintain injury and illness rates below national averages.
- On-Site Consultation Program: Free service for small to medium-sized businesses to help them identify hazards and improve safety without fear of citations or penalties.
- Alliance Program: Collaborates with trade associations, labor unions, and other groups to promote workplace safety through education and outreach.
- SHARP Program (Safety and Health Achievement Recognition Program): For small businesses that operate exemplary safety programs.
These cooperative efforts help reduce the need for enforcement by fostering a culture of safety and proactive compliance.
Employee Rights Under OSHA
Employers bear the primary responsibility for compliance. They are expected to:
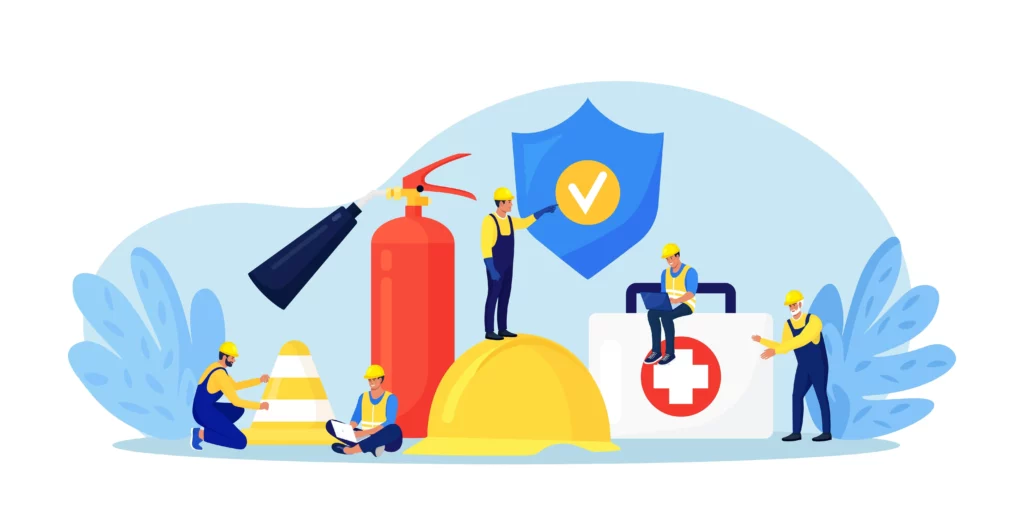
- Identify and eliminate workplace hazards.
- Provide personal protective equipment (PPE).
- Train workers on hazards and how to work safely.
- Keep records of injuries and illnesses.
- Report certain incidents as required.
- Display the official OSHA Job Safety and Health poster in a prominent location.
Compliance is not just a legal requirement — it’s an investment in worker health, morale, and productivity.
Conclusion
OSHA enforces its standards through a balanced approach that includes inspections, citations, penalties, and proactive programs. While its enforcement powers are essential for holding employers accountable, OSHA also prioritizes education, collaboration, and worker engagement. By understanding how OSHA enforces its standards, employers can better prepare for compliance, and employees can become active participants in promoting a safe and healthy workplace.
Ultimately, OSHA’s enforcement efforts save lives, prevent injuries, and create a culture of accountability and care in the American workforce.