Hazard Communication Program Effectiveness
According to the Environmental Protection Agency’s Chemical Data Reporting Program, more than 8,700 chemicals are produced or imported into the United States each year. The purpose of the Hazard Communication (HAZCOM) program is to keep workers safe from chemicals that may lead to illness or injury. So employees should educate themselves on the chemicals that they expose themselves to at work. Workplaces with hazardous chemicals must implement a hazard communication program under OSHA’s Hazard Communication Standard (HCS). So this involves implementing a hazardous chemical inventory. Therefore Safety Data Sheets should be accessible. So workplaces should properly label chemical containers. Employers can implement an effective program of hazard communication by following these six steps,
- Standards for Hazard Communication
- Prepare written Hazard Communication Program
- Proper Labeling on the containers
- Safety Data Sheets
- Train Employees for Hazard Communication
- Program credibility assessment
You can implement an effective Hazard Communication program by using these six simple tools. So it is vital for companies and employers to successfully establish an effective hazard communication to avoid OSHA penalties and fines. So, the Hazard Communication helps the company to operate in a safer and accident-free environment.
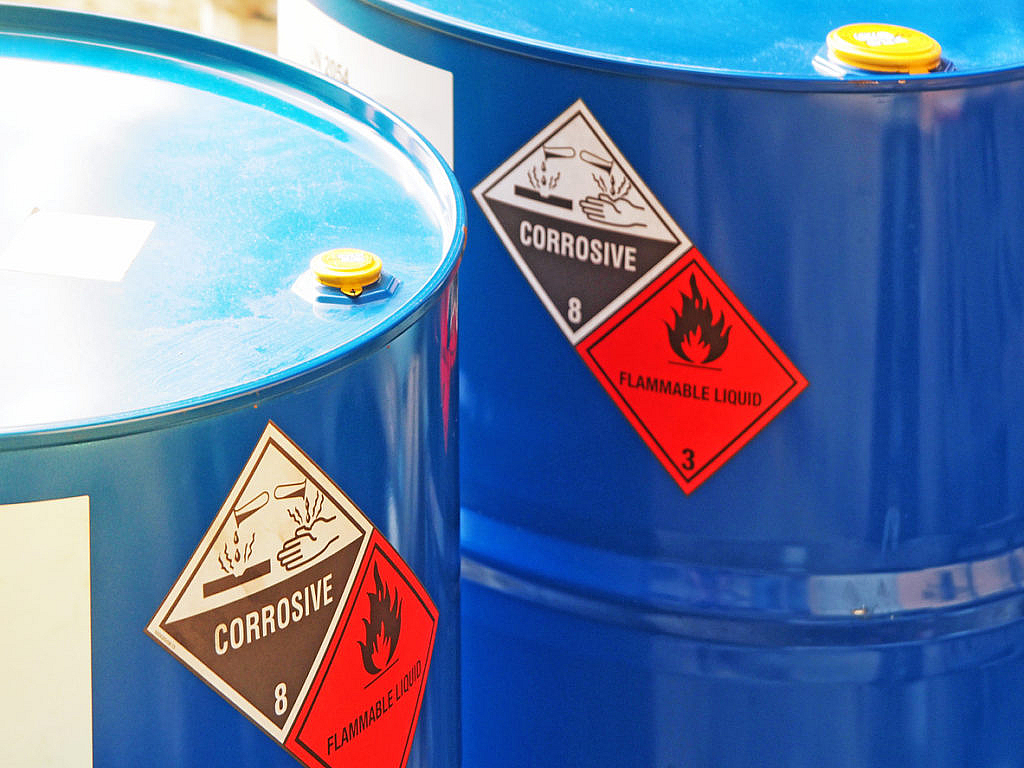
Standards for Hazard Communication Program
HazCom communication is the second most cited OSHA violation in the United States. Even though the hazard communication standards are available on OSHA’s website, it is often ignored by employers. Employers that use chemicals in their workplaces are covered by the standard’s rules on documented hazard communication. The program includes labels, safety data sheets(SDSs), and employee education and training.
You should educate yourself on these regulations to ascertain what is required for compliance in your job. Employers should also designate employees for the implementation of hazard communication. So this will guarantee that your hazard communication program is successful and addresses all key components. The individual is assigned to oversee the program as a whole. Coordination should then assign personnel to certain tasks, such as training.
- Obtain a copy of the Occupational Safety and Health Administration’s Hazard Communication Standard.
- Familiarize yourself with its provisions.
- Assign major responsibility for implementation coordination to someone.
- Assign personnel to specific activities, including exercises, training, etc.

Prepare a written Hazard Communication Program
This process guarantees that all aspects of the Hazard Communication Program are coordinated and comply with the standard systematically. So the written program should describe how the requirements of the labels of paragraphs and other kinds of warning are met; safety data sheets (SDSs); and information and training for staff at work. The stated program also requires companies to keep a list of the known dangerous compounds at work. To construct a list, you may be able to follow the status of SDSs and markers of a specific dangerous chemical by using the product identifier. Recall, the product identification must be the name of the hazardous chemicals that appear on the label and SDS.
- Prepare a documented strategy to show how risk communication in your business is handled.
- Prepare a list or inventory at the workplace of any dangerous compounds for an effective hazard communication program.
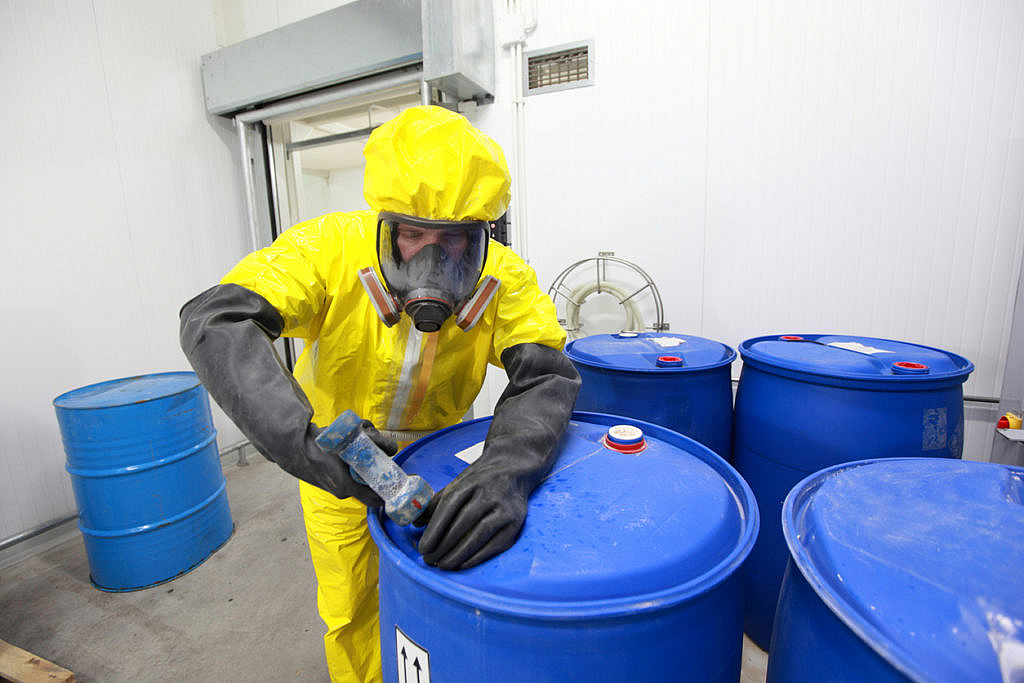
Proper Labeling on the containers
To implement an effective hazard communication program, the following labels must be on all containers: product identity, signal word, pictograms, danger statements, precautionary statements, and the responsible party’s name, address, and phone number. The label thus contains all of this information, although more information may appear. Container labeling is mandatory for employers. In other words, you may use the same label from the supplier or you may mark workplace containers with labels such as “3rd party systems. In addition to the other needed information. Workplace hazardous chemical containers must have at a minimum the product identity and generic information about the chemical’s dangers. A worker must receive full danger information regardless of the approach you choose.
- Always keep shipping labels on containers.
- Require proper labeling of workplace containers.
Safety Data Sheets
Safety data sheets (SDS) provide extensive information about a specific hazardous substance. You should maintain SDS for all hazardous substances found in the workplace. To get an SDS from your provider, just request one. SDSs must be within work area employees’ reach during work shifts. Several options exist for enabling accessibility. Your employer determines what is proper. Some employers maintain the SDSs in a binder in a central place (e.g., in the pick-up truck on a construction site). For others, access to a chemical is provided via a computer network. You must always maintain an electronic backup for SDS. Employees should get familiar with the SDS system. SDS must be readily accessible in the case of a medical emergency.
- Maintain an up-to-date hazard information collection form for each hazardous chemical in the workplace.
- Make sure that all personnel have easy access to any applicable safety data sheets.
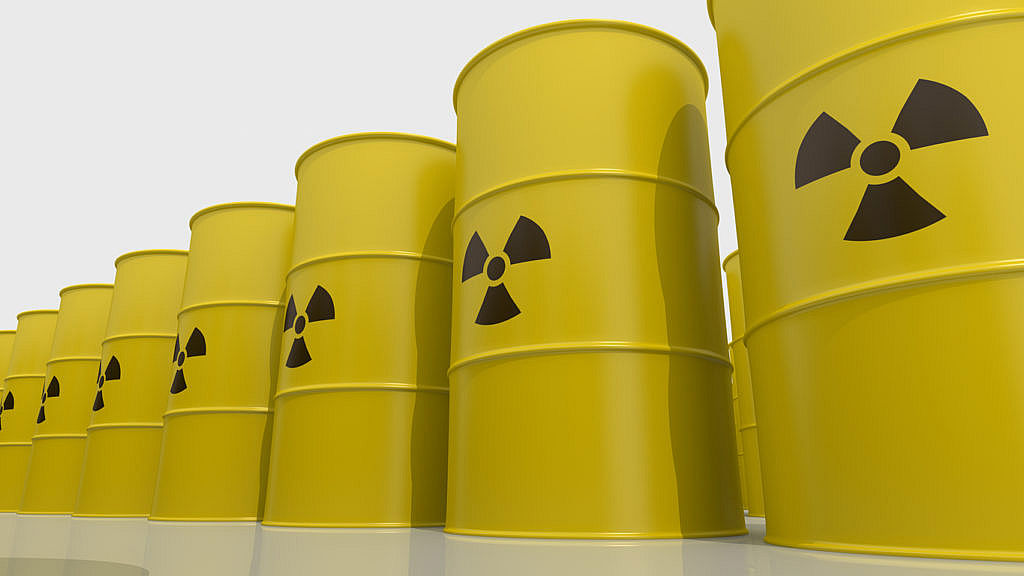
Train Employees for Hazard Communication Program
Employers must ensure their employees get sufficient training on hazardous substances. Enrolling your teams into online HazCom training courses can go a long way in increasing their knowledge about harmful materials. Beyond that, workers should make themselves aware of the risks of exposure to harmful substances. They must realize that safety data sheets and labels contain information about chemical dangers. Furthermore, personnel must be aware of all information available on labels and SDSs, and how to obtain it. The facility must also be aware of the available protective measures, how to use them, and whom to notify in the event of a problem.
- Let the new staff know about all the dangerous compounds they’ll be working with.
- Consider everything that is found in the standard, chemicals’ dangers, and extra safety precautions.
Program credibility assessment
You do not have to reevaluate the hazard communication program; nonetheless, it must be current and relevant to the operation. That’s the best way to do it – you should assess your hazard communication program regularly. Make sure it is still doing its job and continues to accomplish its goals. You should make adjustments as needed to suit changing workplace circumstances (e.g., new chemicals, new hazards, etc.)
- Regularly review your risk communications program to ensure that it continues to operate and its goals are met.
- Review your program accordingly to shifting working circumstances (e.g., new chemicals, new hazards, etc.).
Conclusion
The effectiveness of a Hazard Communication (HAZCOM) program is crucial for maintaining a safe work environment and making sure compliance with OSHA regulations. By following the outlined steps, such as proper labeling, maintaining Safety Data Sheets, and conducting employee training, employers can significantly reduce the risks associated with hazardous chemicals.
Regular program assessments and updates are essential to adapt to new hazards and maintain program relevance. Additionally, enrolling in OSHA training courses can further enhance employees’ understanding and preparedness. Ultimately, a well-implemented HAZCOM program promotes a culture of safety and protects workers from potential chemical-related injuries and illnesses.