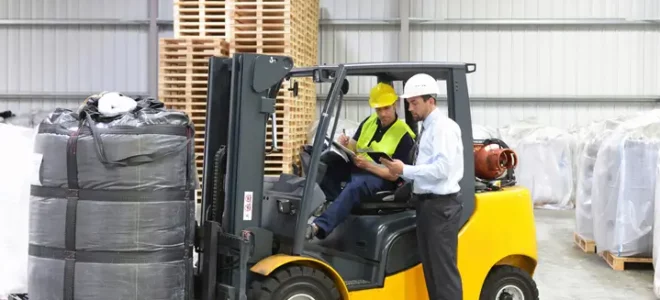
What is a Powered Industrial Truck? How OSHA Explains It
Powered industrial trucks (PITs) are essential powered vehicles commonly used in warehouses, factories, construction sites,
Powered industrial trucks (PITs) are essential powered vehicles commonly used in warehouses, factories, construction sites,
Thousands of workers every year step onto job sites with little knowledge of the risks
Any time we drive, we choose an action that can affect our lives and those
According to the U.S. Bureau of Labor Statistics, tens of thousands of workplace injuries could
In the construction world, safety is non-negotiable. Crane operations, in particular, demand clear communication to
Heat stress is a concerning hazard, particularly in industries involving outdoor or high-temperature environments. According
COMBUSTIBLE DUST Many known materials are hazardous and can also result in big explosions. Combustible
Honoring the Fallen: Reflecting on Workers’ Memorial Day Workers’ Memorial Day is recognized on April
Workplace safety has evolved considerably over the decades; yet, struck-by and caught-between incidents remain stubbornly
Employee safety is of prime importance in every industry in the United States. Most organizations
OSHA’s handrail and stair rail system requirements for general industry have undergone updates to improve
Lithium-ion (Li-ion) batteries are rechargeable batteries that use lithium ions as the primary charge carrier.
Enhance your construction work safety with these 20 essential ‘how-to’ guidelines.
Running a small business involves various responsibilities, including ensuring workplace safety. Many business owners wonder
OSHA Guidelines on Personal Protective Equipment for Construction Workers
Ensuring workplace safety when handling hazardous chemicals is crucial for protecting employees and the environment.
Many people, particularly those who do demanding labor in hot and humid working conditions, suffer