Why Incident Management Matters Suite (WIMM)



Why Workers Choose Us
features | ![]() |
other providers |
---|---|---|
Instant Downloadable Certificate | ||
Free Study Guide
![]() |
||
Discounts For Businesses
![]() |
||
No Hidden Cost | ||
Mobile Compatibility
![]() |
||
Flexible Learning
![]() |
Satisfied Customers
Course Outline
Why Incident Management Matters Introduction
-
1. Why Incident Management Matters Introduction
- Welcome
- What's This About?
- Who's Involved?
- Why ME?
- What's Included?
- What's Next?
WHAT IF? Mentality
-
1. Introduction
- Welcome
- Learning Objectives
-
2. Using "What If?"
- “What If?” in Action
- Why Ask “What If?”
- “What If?” Observations
-
3. Summary
- Summary
Culture of Early Reporting
-
1. Introduction
- Welcome
- Introduction
- Introduction - Outro
- Learning Objectives
-
2. Culture of Early Reporting
- Human Error
- Two Things to Remember About Safety
- Why Early Reporting?
- Why NOT Early Reporting?
- Helping Employees Understand the Value of Early Reporting
- Creating a Culture of Early Reporting: Make-or-Break Factors
- Increasing the Likelihood of Early Reporting
- The Link Between Early Reporting and Learning
- What Does It Look Like When Reporting Results in Learning?
- Ten Dimensions of a Safety Culture
-
3. Summary
- Summary
Inspections and Observations
-
1. Introduction
- Welcome
- Learning Objectives
-
2. Importance of Inspections and Observations
- Terms
- The Role of Reports and Observations
- Why Perform Safety Inspections?
-
3. Perceptions
- Inspection and Observation Perceptions
- Improving Negative Perceptions
- Meeting Your Employees’ Expectations
-
4. Preparation
- Before You Inspect or Observe
- Checklists
-
5. Best Practices
- Good Observer Traits
- During Inspections and Observations
- Observing People Working
- Observing Unsafe Situations
-
6. After an Inspection and Observation
- Inspection and Observation Reports
- Follow-up
-
7. Summary
- Summary
Giving and Receiving Feedback
-
1. Introduction
- Welcome
- Introduction
- Learning Objectives
-
2. Giving and Receiving Feedback
- Receiving Feedback
- Break Bad Habits
- Separate the Feedback from the Person
- Give Feedback Due Consideration
- Start Small
- Giving Feedback
- Effective Feedback Techniques
- Ineffective Feedback
- Be Prepared
-
3. Summary
- Summary
Reporting (Data Entry)
-
1. Introduction
- Welcome
- Learning Objectives
-
2. When to Complete a Report
- What Is Reporting?
-
3. Benefits of Reporting
- Benefits of Reporting Observations and Incidents
- Observation and Incident Reporting in Action
-
4. Effective Reports
- Driving Positive Change
- Report Forms
- Report Narratives
- Report Example
-
5. Summary
- Summary
Incident Investigation
-
1. Introduction
- Welcome
- Introduction
- Learning Objectives
-
2. Concepts and Terms
- Incident Investigation Basics
-
3. Process
- Incident Management and the Investigative Process
-
4. Information Gathering
- Information Gathering
- Interview Best Practices
- Photo/Sketch Best Practices
- Physical Evidence Best Practices
-
5. Benefits
- Benefitting from Investigative Findings
-
6. Causal Analysis
- Causal Analysis
- Asking "Why?"
- Corrective Actions
-
7. Conclusion
- Summary
Tasks and Corrective Actions
-
1. Introduction
- Welcome
- Introduction
- Learning Objectives
-
2. Hazard Controls
- Hierarchy of Hazard Control
- Hierarchy of Hazard Control - Eliminate It
- Hierarchy of Hazard Control - Substitute It
- Hierarchy of Hazard Control - Engineering Controls
- Hierarchy of Hazard Control - Reduce
- Hierarchy of Hazard Control - PPE
- Why Combine Hazard Controls?
- Hazard Controls
-
3. Risk Assessment
- Choosing and Implementing Corrective Actions
-
4. Corrective Actions
- Risk Assessment
- Evaluating and Prioritizing Risks
-
5. Considerations
- Other Factors
- Training and Practice
- Involve Employees in Choices
-
6. Timelines
- Timelines
- Timelines – Best Practices
-
7. Progress
- Monitoring Progress
- Involve Employees in Monitoring
-
8. Summary
- Summary
Trending and Analysis
-
1. Introduction
- Welcome
- Introduction
- Introduction – What It’s All About
- Introduction – Mindset
- Learning Objectives
-
2. Incident Management
- Incident Management
- A Note about Trending and Analysis
-
3. Indicators
- Lagging Indicators
- Trending and Analysis – Lagging Indicators
- Keep Asking WHY
- Leading Indicators
- Trending and Analysis – Leading Indicators
-
4. Follow-Up
- Trending Patterns: A Questioning Mindset
- Example Questions
- Visibility
- Monitor and Follow Up
-
5. Summary
- Summary
Continuously Improve for Safety Excellence
-
1. Introduction
- Welcome
- Introduction
- Learning Objectives
-
2. Define Continuous Improvement
- Continuous Improvement
-
3. Benefits
- Direct Benefits of Continuous Improvement
- Indirect Benefits of Continuous Improvement
-
4. Workflow
- The Continuous Improvement Workflow
-
5. Lagging and Leading Indicators
- Lagging Indicators
- Leading Indicator Benefits
- Leading Indicators – Focus on Activities
- Leading and Lagging Indicators – Better Together
- Making the Shift from Lagging to Leading
-
6. Continuous Improvement in Action
- Continuous Improvement in Action: Before
- Continuous Improvement in Action: After
-
7. Quality Management
- Quality Management Tools
- Quality Management Improves Safety at Airlines
-
8. Summary
- Summary
Group Discount for Corporate Accounts
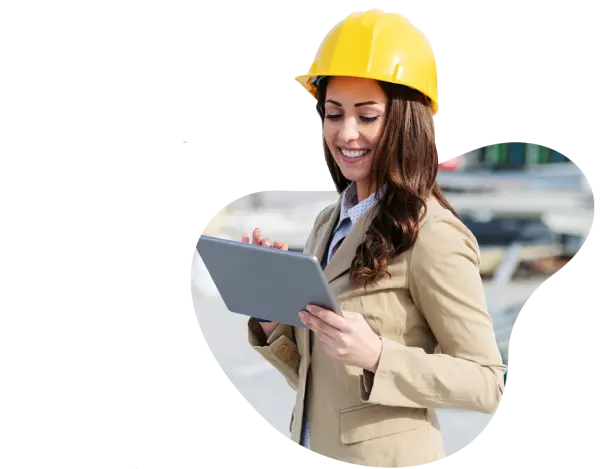
VIDEO TESTIMONIAL
FAQ
What is covered in the Incident Management Importance Training?
What does the WIMM Training Program include?
Is there an Online Incident Management Course available for this program?
What can I expect from the Incident Management Significance Workshop?
How long does the Incident Management Certification course take to complete?
What is the cost of enrolling in Understanding Incident Management Relevance course per seat?
Join our mailing list
Get announcements, industry updates and promotional offers.